
The fingertip has a smooth channel and the "ball" that runs in the socket. The part around the base of the finger has clearance for the wire to move when the finger bends. A flexible wire pulls the joint together. The first joint consists of a sort of ball and socket design. While I would be able to design this and make this, it would make replicating this project problematic. I suspect he uses a coil spring, potentially with a cable running through it as a hinge. While technical details are not shared (he sells them after all) it is clear that he uses some type of living (or bending) hinge. Gary Fey seems to have encountered this problem as well, and made some sort of living hinge. This hinge was still quite large, fragile, and difficult to print. I first tried making the hinge as a conventional hinge (as seen in the photo). This forces the hinge to be fairly narrow. There are also up to two fingers, one on each side, sitting very close to the hinge. While most hinges on the extensions have width available to them, around the finger there is a finger in the way. The first hinge around the finger is the most challenging part of the design. The joint right after the gears was split up into 3 pieces in order to make it printable. All gears and linkages are printed flat on the bed. This makes it simpler to print due to limited overhang, and gives all joints room to move 90 degrees. In order to keep the design itself calm, I wanted all finger joints printed in the same orientation. The same goes for all other finger joints, which need to move past each other. The ring at the base of the finger also needs to accommodate the almost 90 degree motion of the finger itself, forcing it to have a 45 degree angle. Printing them on the side would give difficult bridges to print. Given that all fingers have some sort of linkage running through them, this kind of forces me to print all finger related parts upright. This means that all parts cannot have overhangs greater than roughly 45 degrees, and only short bridges. One of the main reasons to make my own design is to try and make it support free. These will hopefully help people understand some of the choices I made, and maybe aid people trying to design this themselves. There are a few design choices that I do want to share with the people making this mechanism. This Instructable is my first prototype of supportless articulated finger extensions. Make the design match my scales (not in this Ible).I hate supports on mechanical parts, and felt it would be possible to make a design without supports. This basically requires the Gary Fey puller design. Make the extension's movement happen in as close as 90 degrees of finger movement as possible.Make the design easily modifiable so I can alter it to my hands (and anyone else's if I do it right).It worked fairly okay, but I would have wanted better measurements to determine what I needed to print.Īfter printing the single finger I wanted to try designing it myself. There was no real information on the dimensions, so I had to print a random size and hope. The style did not really match with anything I wanted, but that is not a valid complaint. It also tended to bind a bit because of how the linkages are placed.
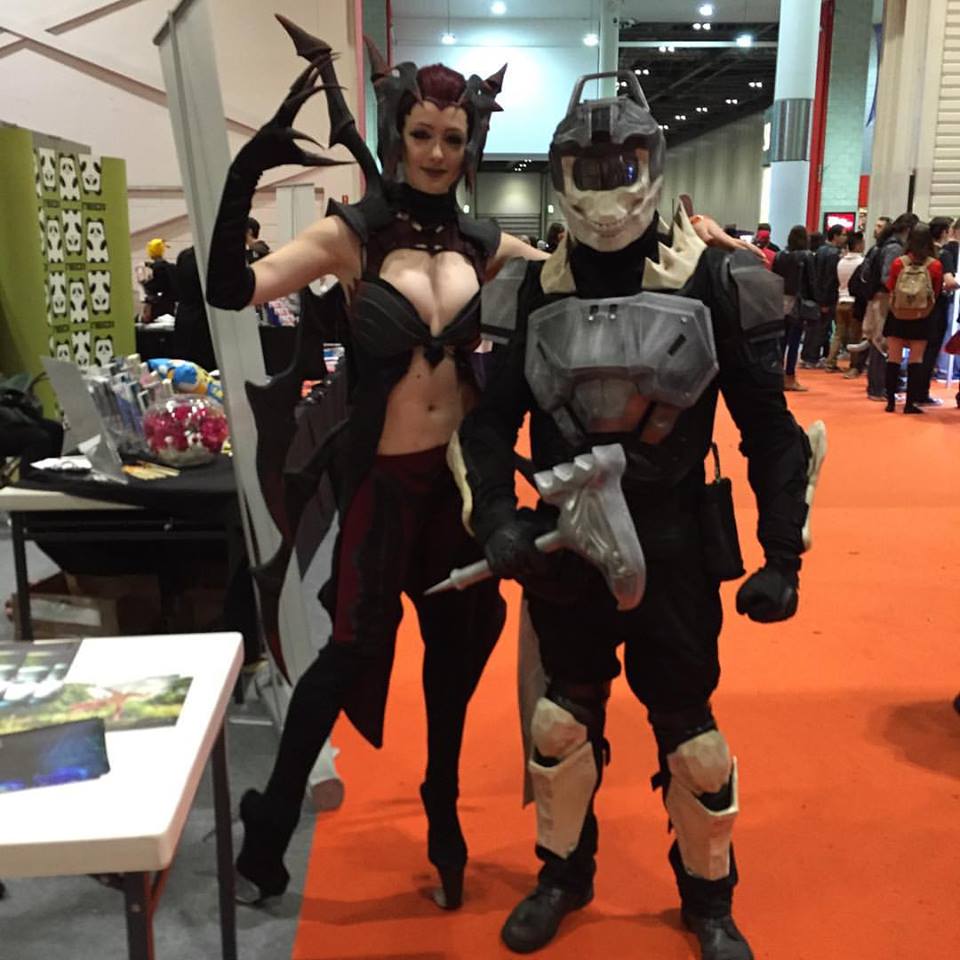
While it was somewhat optimized for 3D printing, it was a supported print.

COSPLAY 3D PRINT FILES FULL
My finger can only move by 45 degrees for the full movement of the extension.
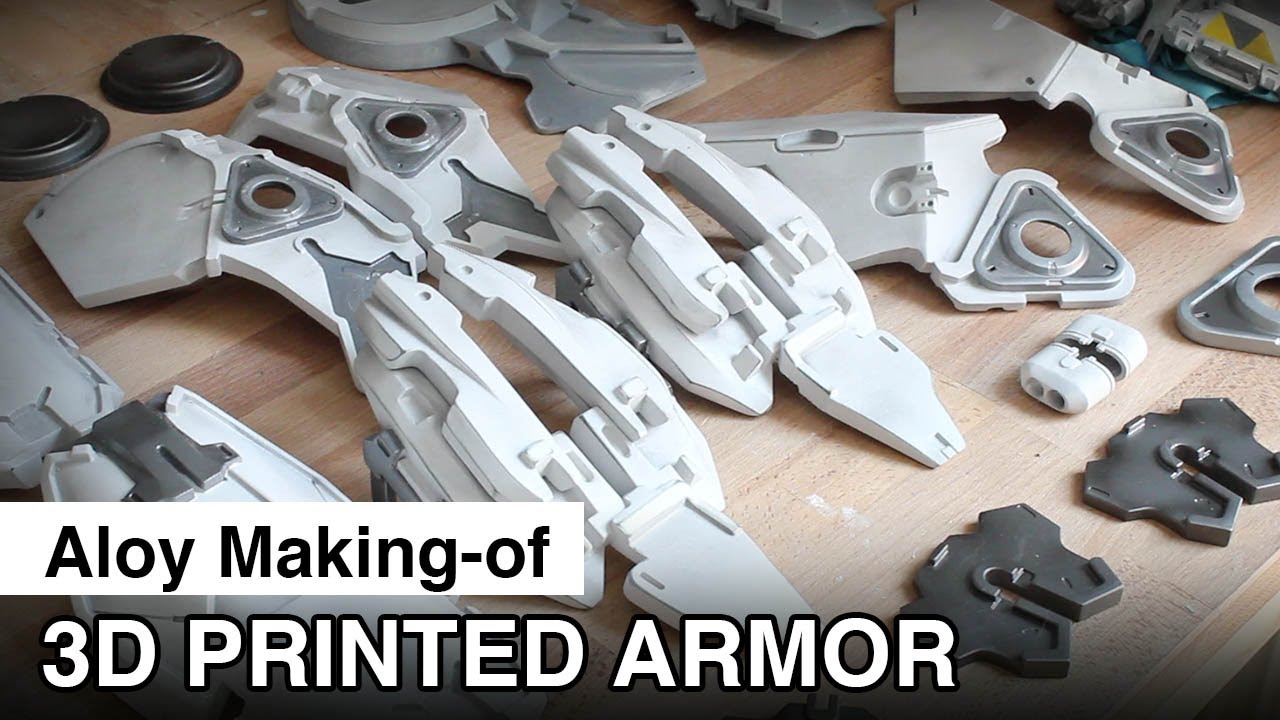
It is a pusher system which is a bit limiting in the movement, and places push bars on the inside of the hand. In my case, robot, but there is also dragon and skeleton. It is a design that has the style in the part itself. The second is a model you have to pay for on Cults3d. It was also one I did not try myself, because I found something else first. It is brilliantly compact, seems to work well, and should be a decent print. It is designed to be as compact as possible, and the be reskinned with another file. These finger extensions were more closely resembling the model by Gary Fey, using a pulling system on the top of the finger (more in the next step). Gary Fey, the creator of the vingers in the first video only sells the fingers themselves. Why design something that already exists. I started looking around the internet to find existing plans. Preferably one that matched the 3D printed scales I already have ( link to scales). As is often the case, I vaguely remember it, and rediscover it later with more passion.Ī few weeks ago was when I got that passion. My first encounter with the articulated finger mechanism was when I saw them on Tested ( video) where Adam Savage showcased them. Why did I make this? First of all, because I can and they are awesome.
